Fiber optic technicians deploying the network of Swisscom, the leading telecom operator in Switzerland, leverage Deepomatic to control the quality of their daily tasks. Dive deeper into their journey by watching an exclusive interview with a technician from Cablex, a subsidiary of Swisscom. Discover how Deepomatic enhances its efficiency in deploying fiber optic operations.
A Smooth User Experience For Fiber Optic Technicians
Deepomatic, integrated with Cablexâs internal Field Service Management (QS App), aims to simplify the quality control workflow of field service engineers. The QS App provides the technician with a comprehensive overview of their assigned sites, ongoing projects, and critical information such as Building Entry Point (BEP) type, mini cable, and splitter count. The technician accesses a checklist of all the tasks they must perform and uses their smartphone or tabletâs camera to capture images of the piece of equipment right before working on it and after completing their tasks.
Deepomaticâs visual inspection system analyzes these images in real-time, providing immediate feedback by displaying green lights for correctly executed tasks. If the AI finds a checkpoint ânot in order,â it flags it, allowing the fiber optic technician to address the issue promptly before leaving the site. Once they have fixed the error, they take another photo that the system analyzes, demonstrating that they have completed their work correctly.
Advantages for Fiber Optic Technicians and Their Companies
Integrating Deepomaticâs computer vision brings numerous advantages to fiber optic workers and employers. Letâs examine some benefits:
Complete quality controls and standard compliance
Field service engineers can perform thorough quality controls after installations, ensuring the fiber networks meet the required standards. By getting information about the quality of their work, they can learn from errors and improve their gestures as they go. The reduced rate of errors eliminates the need for truck rolls and streamlines the finalization of the network, ultimately enhancing technician efficiency.
Reduced operational costs and improved customer satisfaction
Employers benefit from reduced operational costs and improved customer satisfaction. The efficient installation process minimizes delays and rework, leading to cost savings. Additionally, our platform compiles all installation data into easy-to-read KPI dashboards, providing valuable insights for informed decision-making.â
Addressing Connectivity Challenges in Fiber Optic Installations
While Deepomaticâs platform significantly boosts productivity, it is crucial to address the challenge of limited internet connectivity in some areas. Fiber optic technicians often encounter situations where an internet connection is not readily available on their tablets or smartphones. To mitigate this issue, technicians can capture images offline, step out of the area to acquire reception, and then automatically load the photos into the app once they establish a connection.
The integration of Deepomaticâs computer vision technology has revolutionized the work of Swisscom and its subsidiary fiber optic engineers. With real-time feedback and streamlined quality control, the platform ensures efficient fiber connections while maintaining service excellence. The advantages offered by Deepomatic, such as comprehensive quality control and reduced operational costs, are advantageous for technicians and employers alike. Working alongside telecom operators of many countries also showed us how important the user experience of field workers is to drive their adoption of the technology.
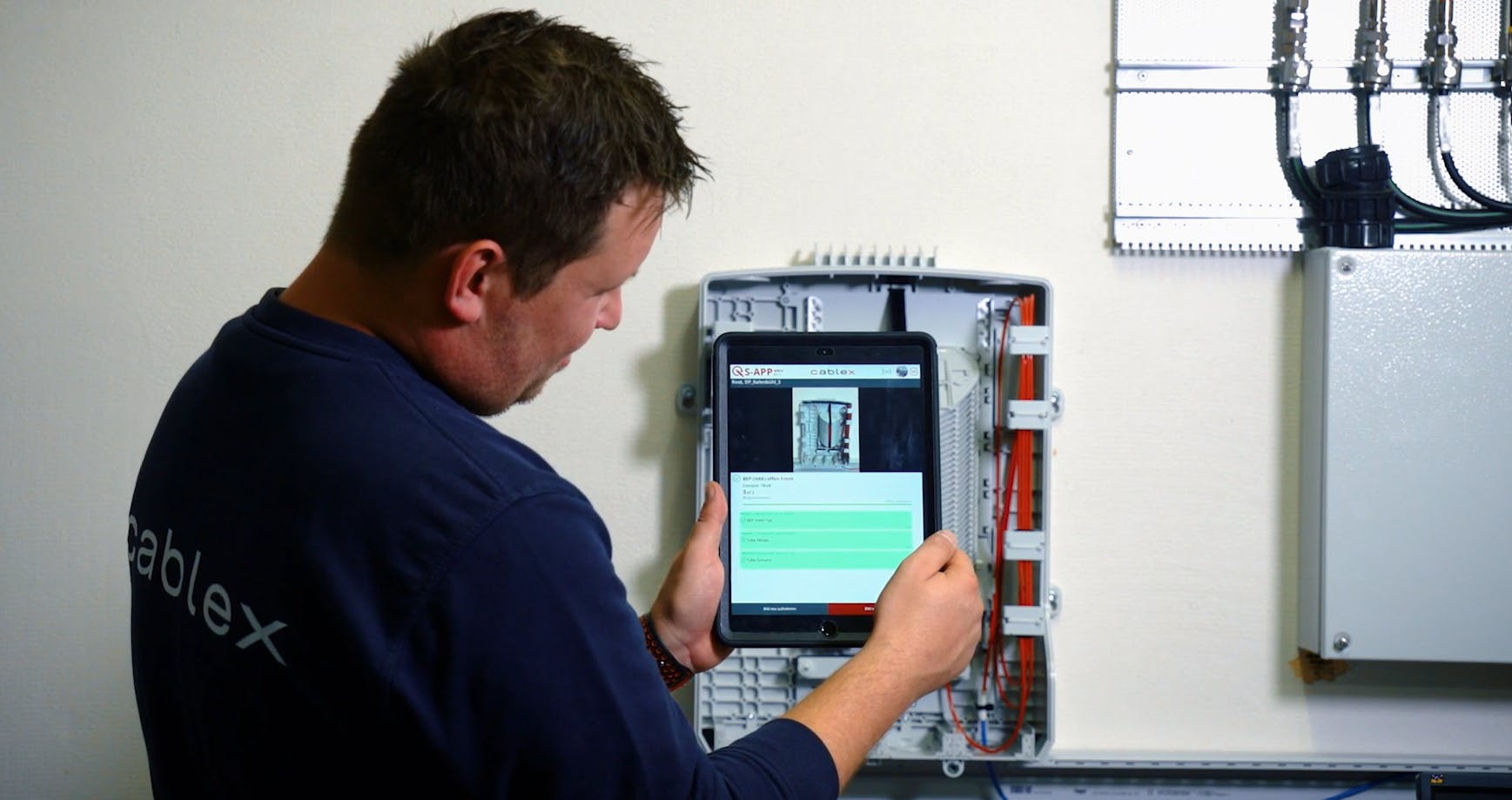
FAQ
1. Does Deepomatic provide a standalone app?
Yes, we offer a mobile web app that our clients can deploy and easily incorporate into their existing user journey through a one-click integration. The field worker can start their journey on the existing tool (FSM, GIS, etc.), and at each job step they have to perform, they can click on one button that redirects them to the Deepomatic app to take the pictures and get the AI results. This removes the need for our clients to create a user experience for the quality control process in the field.
2. How does Deepomaticâs computer vision platform ensure accurate quality control?
Deepomaticâs computer vision platform utilizes advanced algorithms to analyze images captured by technicians. We train these algorithms to identify specific checkpoints and flag any inconsistencies or issues. This real-time feedback enables technicians to address problems immediately, ensuring accurate quality control throughout the installation.
3. Can Deepomatic customize its computer vision technology to meet specific company requirements?
Absolutely! Companies can collaborate with Deepomatic to establish their desired checkpoints, further enhancing quality control methods. Our customers can build and implement new models by providing a dataset of images and defining specific checkpoints.Â
4. How does Deepomatic handle potential disruptions caused by a lack of connection?
We have adapted our user experience to inform fiber optic technicians in the app when they lack a connection. Once they establish a connection, they can load the images captured offline into the app. This flexibility ensures that field service engineers can seamlessly work in various environments and adapt their use of the tool in case they meet connectivity issues.
5. How can Deepomaticâs computer vision technology benefit other industries besides fiber optic installations?
The versatility of Deepomaticâs computer vision solutions enables their implementation in various industries beyond fiber optic installations. Companies can leverage the technology in utilities, Emobility, healthcare, and more, to enhance operational efficiency, quality control, and overall performance.