Swisscom & Deepomatic: Implementing Visual AI in the Entire Fiber Roll-out Journey
Swisscom, the leading fiber optic infrastructure operator in Switzerland, aims to expand its fiber-optic network significantly. By the end of 2025, coverage is expected to rise from 47% to 57%, and by 2030, it should reach 75-80%.
Today, Swisscom relies on four contractors for fiber roll-out and electricians for fiber service activation. With increasing field operations and a commitment to providing top-quality service to subscribers, Swisscom seeks to ensure every fiber optic installation meets their high standards. They partnered with Deepomatic, the leader in First Time Right Automation using computer vision technology.
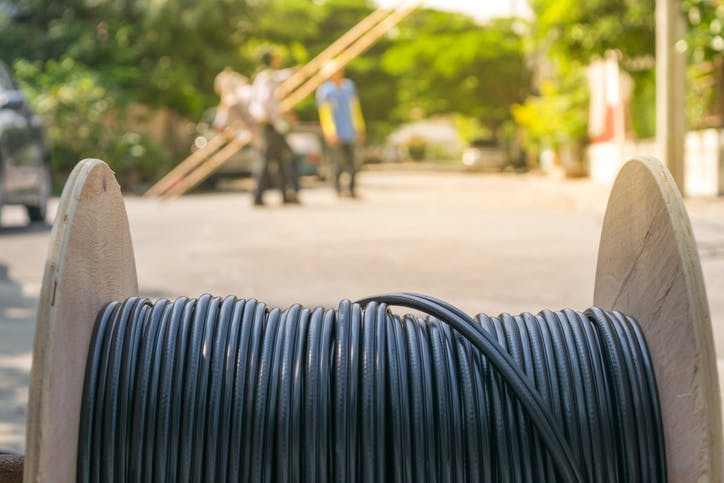
Thanks to this partnership, Swisscom has successfully managed to:
- Increase its operations First Time Right rate, ensuring technicians succeed on their first visit.
- Automate the quality control process to scale efficiently and reduce the need for field audits.
- Ensure photo documentation from technicians was complete and reliable.
- Empower technicians with self-learning capabilities.
- Base subcontractor payments on verified proof of quality work.
Over the past two years, five applications were progressively deployed in the FTTx journey:
Central office equipment installation
Fiber manhole state, safety, and cleanliness
Sleeve installation
In-house connection of the Building Entry Point to the network and fiber installation
Subscriber connection to fiber
Two additional applications will be deployed soon:
Preventive maintenance for poles
Connections in the Central Office
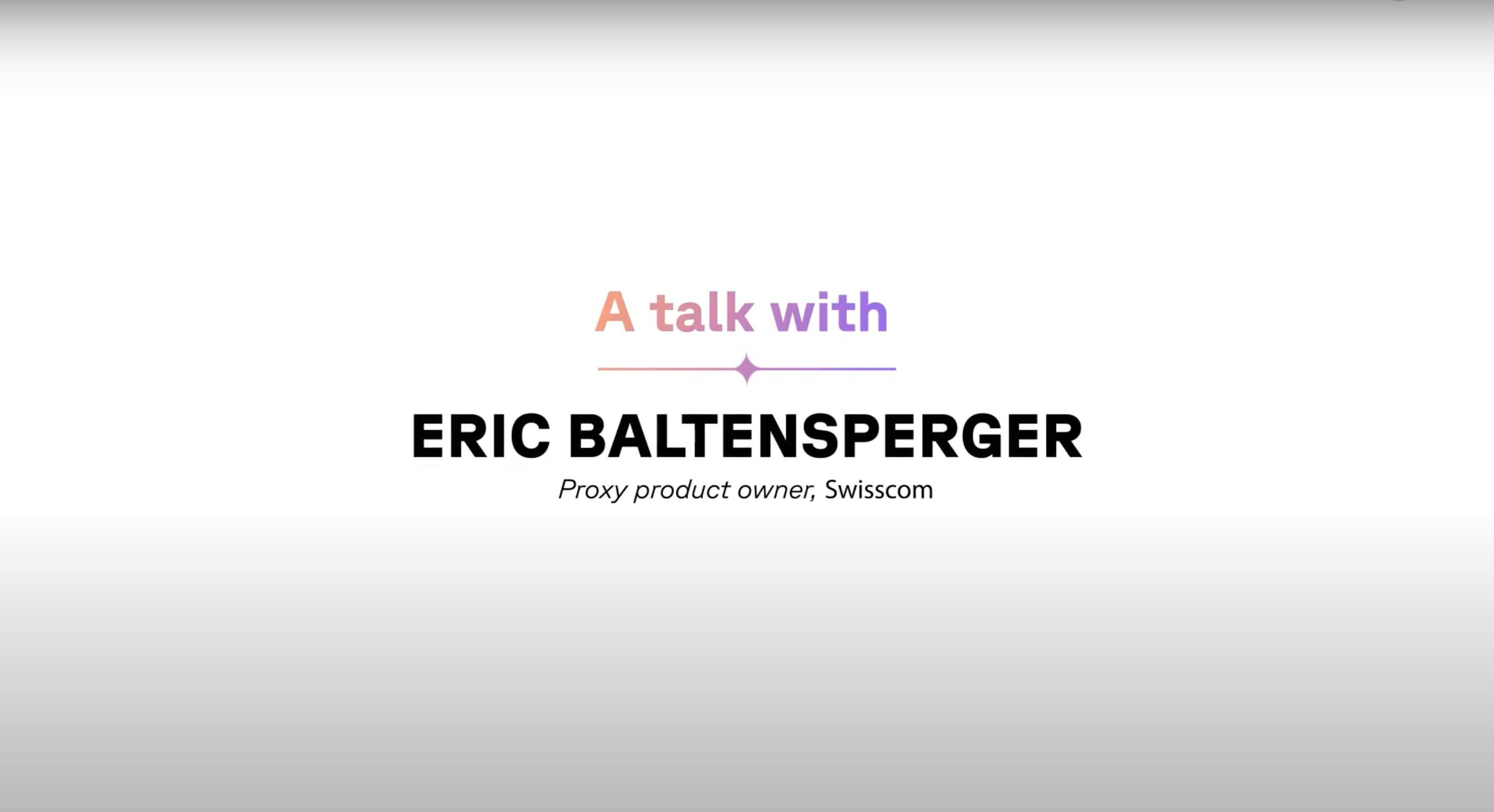
Before Deepomatic
- Manual verification of 10 to 20% of operations, selected randomly
- Excessive time spent on manual quality control
With Deepomatic
- 100% of operations checked by the AI: real-time verification of photos (context, angle, brightness) and conformity checks of technicians' work through a series of checkpoints.
- Technicians can immediately correct potential anomalies, ensuring the job is done correctly before leaving the site.
- Swisscom back-office and management teams access high level KPIs on the quality of the operations
- Automatic acceptance of fieldwork triggers contractor payments.
100%
of operations well documented with all images
X3
Increase in quality control capacity with AI
95%
First Time Right rate of fiber operations
Deepomatic has drastically improved cost efficiency for Swisscom. Without the Visual AI platform, expanding the fiber roll-out would have required hiring hundreds of back-office staff for spot checks.
"Quality controls in network construction using artificial intelligence are a central and important lever for Swisscom. Deepomatic not only improves construction quality, but also enhances the customer experience thanks to a higher rate of correctly completed work ("first time right") and fewer interventions on site. Direct feedback allows installers to learn independently and continuously, contributing to cost savings” said Ralf Gugelmann, Head of Rollout, Maintenance & Single Project at Swisscom.
“The use of Deepomatic promotes the digitalization and automation of network construction processes. It also enables us to better compare the quality of on-site work by all construction partners through benchmarking options without needing to be on-site ourselves.”
Ralf GugelmannHead of Rollout, Maintenance & Single ProjectSwisscomVisualize the project between Swisscom and Deepomatic!
Need to see how Deepomatic's solution is used by Swisscom in its fiber optic deployment journey?
From central office, distribution points, to in-house and fiber installation operations, take a look at our infographic to see our First Time Right Automation platform in action!
Discover the infographic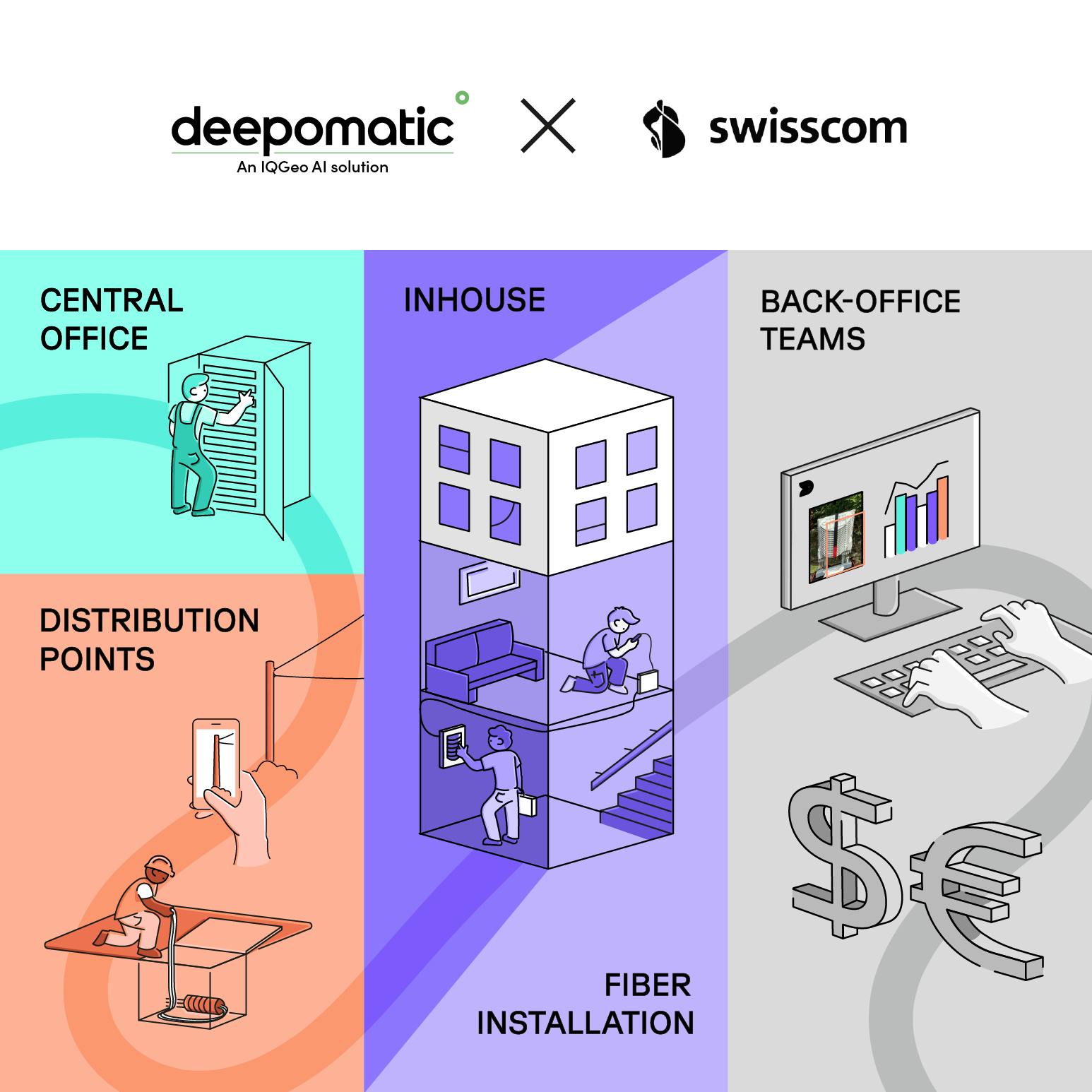