Can you tell us a few words about TDF and your role within TDF's Fiber Business Unit?
TDF is a telecommunications and broadcasting wholesale carrier providing digital coverage across France, generating nearly 770 million euros in revenue in 2021. The company currently employs approximately 1500 collaborators and specializes in mobile networks, television and radio broadcasting, as well as fiber optic networks. We entered this latter market five years ago.
I work as a Product Management Officer in the Transformation Department of the fiber business unit, a team in charge of all the processes and methods. One of my missions has been to introduce artificial intelligence into our processes. In this capacity, I oversee the use of Deepomatic’s platform.
If we focus on the optical fiber sector, what challenges is TDF facing?
TDF, through its five subsidiaries, deploys, markets, and operates the fibre optic network in six French departments: Val d'Oise, Yvelines, Indre-et-Loire, Loir-et-Cher, Maine-et-Loire, and Haute Savoie.
760,500 optical connections will thus be deployed in partnership with local authorities and marketed by internet service providers.
The final connection of subscribers to the network is the responsibility of the Internet Service Providers (ISPs) Bouygues-Télécom, Free, Orange, and SFR, who subcontract these operations.
There is currently a major issue regarding the quality of these connections. This issue is closely monitored by the government, and the regulator (ARCEP) has imposed a regulatory framework on Internet Service Providers. Bouygues-Télécom, Free, Orange, and SFR are required to systematically provide infrastructure operators (wholesale carriers) with operation reports that include photos of the relevant infrastructure taken by technicians when they connect the subscriber. This is how the introduction of AI-powered photo analysis, specifically computer vision, became necessary to verify the quality of connections.
Beyond the quality of connections, if we want to ensure the sustainability of our infrastructure, we also need to monitor the lifespan of the network. The second challenge is, therefore, to monitor the degradation of equipment in the medium to long term and thus guarantee the profitability of TDF's investments in its fiber infrastructure.
You mentioned quality issues; what are the consequences for TDF?
Very concretely, the technician is paid when they connect a subscriber to fibre, so he has every interest in being quick in his mission. Unfortunately, this is sometimes at the expense of the quality of his work. This is how many defects are observed. When the work is not done properly and this type of operation multiplies, there is a domino effect: as installations succeed one another (sometimes very quickly), we end up with messy street cabinets...This is when we declare the defects, and this leads to costly repeat visits for the subcontractor or the Internet Service Provider.
On our side (TDF), if we are not able to stop this type of phenomenon, we end up planning total repairing operations of street cabinets, which can be estimated at around €4000 per cabinet. Those repairing operations involve internal resources, even if the operations are subcontracted.
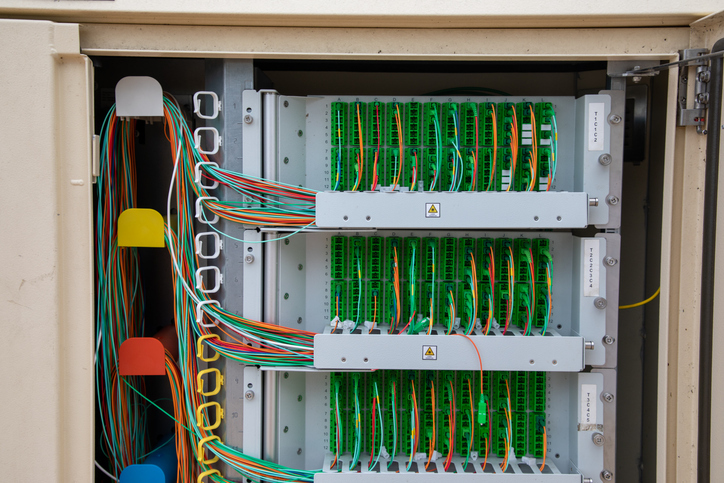
What was the quality control process before the implementation of the Deepomatic solution?
Throughout the deployment period of our networks, site managers are in the field, and auditors are responsible for checking the quality of operations.
Regarding connections, there was no systematic control procedure. Random checks or field reports were used to identify defects and/or deteriorations. The growth in the number of connections required the implementation of an industrial and systematic solution. Finally, the Fiber BU's exploitation department organized preventive maintenance, with two visits per year to each of our street cabinets.
So you chose to use Deepomatic to scale up quality control?
Exactly! We have been in contact since 2021. After a POC in 2022, we chose Deepomatic’s computer vision platform, which analyzes the photos of each operation report made available to us by the ISPs operating on our networks.
Who currently uses the Deepomatic solution at TDF, and how do you utilize the business intelligence data?
At this stage, I provide regular reporting to the Operations department. The KPI results are diverse and are addressed to various collaborators on the Ops team, depending on their respective responsibilities. For example, we have established indicators with Deepomatic regarding the completeness of the operation reports (provided photos), the exploitability of the photos, the quality of the connections, and the observed defects, as well as the fiber termination point references (labeling) in line with the optical route provided by TDF to the ISP.
TDF collaborators who manage the relationship with the ISPs use Deepomatic and rely on the results I provide to report defects to the ISPs. They can thus ask them to come back again to repair the equipment on which the technician did not adhere to the rules.
The Ops managers also have access to the platform. Thanks to the degradation index, they get data that allows them to know the state of our infrastructure, especially the street cabinets. This allows them to trigger corrective maintenance when it is needed.
Regarding the tools/interfaces of Deepomatic’s platform, the Search function is the suitable tool to retrieve a given operation report and check the quality of the connection for each piece of equipment. The Asset Management functionality is very relevant to check the state of equipment, especially since it allows us to go back in time and track its evolution, report after report, if necessary. Finally, the Intelligence Center is very useful for performance indicators, such as the volumes of operation reports processed over a given period or, for example, the compliance rate or completeness rate of those reports.
Have you been able to measure the impact since the implementation of the project with Deepomatic? What benefits do you derive from this project?
The first benefit is related to regulation compliance since we communicate fiber connection KPIs to ARCEP. We rely on the results of the operation report analysis on the Deepomatic platform for some of them.
Since the implementation of Deepomatic’s computer vision platform and the sharing of results with the ISPs, we have observed a very clear improvement in the completeness of the operation reports as well as the quality of the photos provided by technicians. It should be noted that all wholesale carriers and ISPs have introduced AI and thus contribute to improving results.
Deepomatic’s platform integrates data related to the activity of ISPs as well as the state of our infrastructure. We rely on it for the repair of the street cabinets.
We also intend to reduce our preventive and corrective maintenance costs through more efficient piloting using Deepomatic’s platform, where we can always follow the state of our equipment.
AI replaces our eyes when we are not in the field!
A few words about the collaboration with Deepomatic to conclude this interview?
The Deepomatic teams are involved and responsive. Deepomatic collaborators are also proactive. A relationship of trust has been established. This is obviously very important for TDF, especially because it is necessary to continue improving the results of certain checkpoints. It also allows us to make the platform evolve, to keep it relevant as our business needs change.