Companies deploying AI and automated systems are not just doing it for the brand image; they genuinely expect tangible value, such as increased efficiency and revenue, within a reasonable time frame.
AI initiatives now focus on real-world impact rather than merely appearing innovative, particularly in reducing human error. Field operations companies that deploy computer vision to automate their quality control process make no exception: maximizing their ROI is the number one priority.
If your goal is to fully capture the value of QC automation, it's essential to establish a strong baseline, continuously monitor progress, and evaluate long-term results using both quantitative and qualitative indicators. This approach ensures sustained success.
In this blog, we’re going to explore how to effectively measure the value of your QC automation project using these integrated indicators, providing you with a comprehensive framework for evaluation.

Setting the Baseline for Your Quality Control Automation Assessment
Defining and Measuring Your Operational Efficiency Metrics
In field operations, quantitative metrics establish a baseline for evaluating the impact of your automated quality control solution. This is done by analyzing productivity and financial metrics like:
- Baseline error rates in field operations leading to revisits. The Total Economic Impact™ of Deepomatic revealed that on average, before deploying our quality automation platform, companies were experiencing a 10% error rate in their field operations.
- Number of on-site audits, with associated labor costs
- Number of operations manually checked in the back-office with the associated time and labor costs. One of Deepomatic’s clients in Ireland reported inspection times of around 10 minutes for deploying smart electricity meters before implementing automated quality control, while another client rolling out fiber optic in the UK experienced inspection times of up to an hour for more complex cases.
- Number of calls between technicians and service center, with the associated labor costs
- Penalties due to lack of compliance in field operations
Tracking these is crucial because they provide a clear picture of current performance and help you identify areas for improvement within your automated quality control system.
User readiness
This involves subjective assessments that capture user experiences and perceptions, such as worker readiness and training feedback. It’s an assessment that addresses the human aspects of automation. Questions such as those below can lift the hood of an automated quality control system and reveal the nuts and bolts of the user experience.
- How effective was the training in preparing you to use the new system?
- What aspects of the training were most helpful, and which could be improved?
- What challenges, if any, did you face during the initial training?
With these insights, you can gauge how well the new system is being received and identify any potential areas of improvement in automated quality management.
Monitoring the First Impacts of Quality Control Automation
Once the wheels of the project are turning, your field operation company will need to actively monitor progress to ensure you are on track to meet your goals. This can be facilitated by automated quality inspection systems.
While some indicators might require at least 6 months of a project run in order to reveal the impact of quality control automation, you will witness some concrete results after just a few weeks of deployment.
Quality Control Scalability
After the solution is fully deployed, the AI-powered inspection process automatically checks 100% of operations that happen in the field, ensuring thorough quality inspections.
This accomplishment is significant, given that conventional manual inspections usually check only 10% of operations. As a result, many potential errors are missed, revealing the inefficiencies inherent in manual inspections.
Documentation Quality
At Deepomatic, documentation quality checkpoints are the first measures we implement with our clients. Because they are implemented early on, these checkpoints quickly start delivering value to our clients. Automated quality control systems ensure that documentation quality is consistently high, providing immediate value upon deployment.
Photo report completeness
This indicates the percentage of operations containing the required number of photos. Typically, this is a metric that improves very quickly after the deployment of the quality control solution in the field. With this data, we can quickly start delivering value to our clients by implementing documentation quality checkpoints early in the process.
Photo conformity
Photo conformity checkpoints ensure that photos are well-framed, not blurry, and taken with the correct level of luminosity. Thanks to the live feedback provided on those checkpoints, field workers know when they have to retake better photos that meet expectations, and this is why companies quickly witness higher photo conformity rates. For example, Movistar Colombia improved its documentation conformity rate to 98% within one month.
Measuring The Success of Your Quality Control Automation Project Over Time
To accurately assess the impact of an AI-powered quality control automation project, we recommend allowing the project to run for at least 6 months, preferably 1 year. This time frame ensures that all desired checkpoints can be fully deployed and provides enough time for the AI to ramp up and deliver tangible results.
Cost savings thanks to greater operational efficiency
A Forrester study on the Total Economic Impact™ of Deepomatic revealed that implementing our automated quality control solution in field operations resulted in substantial cost savings.
- Error rate reductions thanks to higher job conformity: passing from 10% of operations with errors requiring revisits, to 5.5% after 3 years.
- Back-office human audits decreased: from 15% to 1% after 3 years
- On-site human audits decrease: from 10% to 1% after 3 years
In the TEI of Deepomatic, these benefits represent cost savings of almost $5M on average for companies over 3 years, and a 423% ROI.
For more information about those results, check the full study of Deepomatic's TEI.
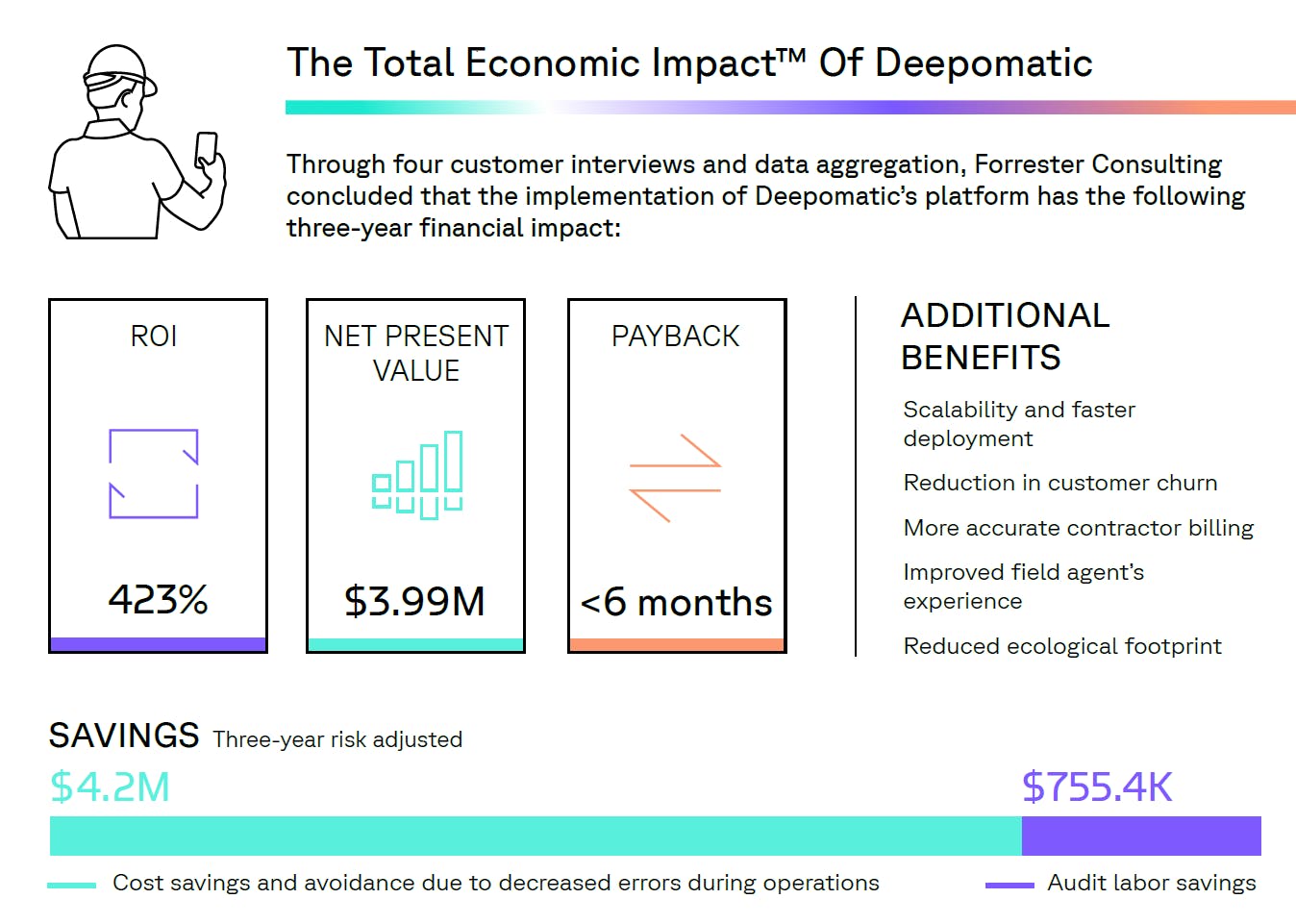
Additionally, the drop in errors in field operations directly impacts the number of revisits, showcasing the effectiveness of improved quality control processes. For instance, Movistar Colombia observed a 21% decrease in its revisit rate thanks to real-time quality control.
Improved documentation accuracy can also generate important cost savings. Indeed, inaccurate reports provided by contractors can lead to an overbilling for operators. In the case of Vodafone Spain, using AI to verify the photos provided by the contractors enabled the company to reduce its fiber installation cost by 20%.
Below are the quantitative metrics that other companies have achieved using Deepomatic.

Revenue generation and protection
But QC automation is not just about cost savings, it can also be a revenue generation catalyzer for field operation companies through enhanced automated quality inspection. By automating their quality control process and therefore improving the quality of their operations, companies can also:
- secure more business contracts through high-quality work.
- Reduce customer churn by improving service reliability.
- Increase revenue through customer loyalty and referrals.
- Increase revenue by running more operations, thanks to the reduction of time dedicated to revisits in the field.
An improved quality in field operations also helps reduce the amount of penalties received for non-compliance issues
Finally, thanks to a higher quality of work during field operations, companies can protect the long-term sustainability of the infrastructures. Consequently, this protects their future operational reliability and therefore the future revenues of companies that own them.
Field workers’ upskilling
Additionally, continuous worker upskilling from real-time feedback leads to fewer errors and better problem-solving, which in turn enhances overall productivity and operational efficiency.
As workers receive immediate insights into their performance, they are able to make adjustments on the spot, reducing the likelihood of recurring mistakes. This ongoing development fosters a culture of continuous learning and improvement, which also contributes to higher employee satisfaction and retention.
What’s more, when workers feel empowered and supported in their roles, they are more likely to take ownership of their tasks and proactively address challenges. This ultimately leads to a more resilient and adaptive workforce, further optimizing automated quality control processes.

In conclusion, quantifying the value of your quality Control automation project in field operations is not just about tracking immediate improvements—it's about understanding and leveraging the full spectrum of long-term benefits that automation can bring.
From initial efficiency gains and cost savings to enhanced revenue generation and workforce development, the true value of automation lies in its ability to transform your operations sustainably. In any industry, this will drive product quality and customer satisfaction.
By setting clear baselines, actively monitoring progress, and measuring long-term success through both quantitative and qualitative indicators, companies can ensure that their investment in QC automation yields substantial, ongoing returns.
This holistic approach not only maximizes ROI but also drives continuous improvement, positioning your company for sustained success in an increasingly competitive landscape.