With Camera Connector, Deepomatic expands its integration capabilities, enabling field service businesses to seamlessly incorporate its automated quality control solution (First Time Right Automation) into their existing field applications. For technicians, it means accessing the full power of the solution through the Deepomatic mobile app, which incorporates a journey adapted to their workflow. This contributes to the successful unfolding of operations and allows companies to obtain reliable, comprehensive field reporting.
Turnkey user journey to support technicians
As AI plays a pivotal role in on-field quality control processes, technicians are now responsible for providing data to fuel the system, including photos of the equipment they work on. Addressing this shift in their role is precisely what Camera Connector does. This connector allows businesses to effortlessly integrate the automated quality control solution into their existing field tools, capitalizing on the real-time photo-taking and quality control process developed by Deepomatic. The solution seamlessly fits into the technician's workflow, ensuring a smooth experience that doesn't hinder the use of the solution.
What does this Technician-AI experience entail? When accessing the list of intervention steps in their usual field application, technicians click a button to switch to Deepomatic's mobile web app to capture equipment photos. Initially, the solution analyzes the photo quality and notifies the technician of rejection, specifying the reason (blurry picture, insufficient brightness, poorly framed, not showing the expected element). The technician is prompted to retake the photo. Subsequently, they receive the AI analysis result on the conformity of their work. Control points are directly outlined on the image for the technician to identify, with textual explanations provided if some are invalidated. The technician can access examples of photos where these control points are validated to understand the expected result of their work. Finally, the application also allows the technician to explain when the AI rejects a control point, justifying the rejection of a step that may not be their responsibility.
By implementing Deepomatic's automated quality control solution via Camera Connector, field service companies deploy an optimal photo-taking and quality control journey, facilitating the technician's work. This saves them from developing this process in-house by mobilizing internal resources.
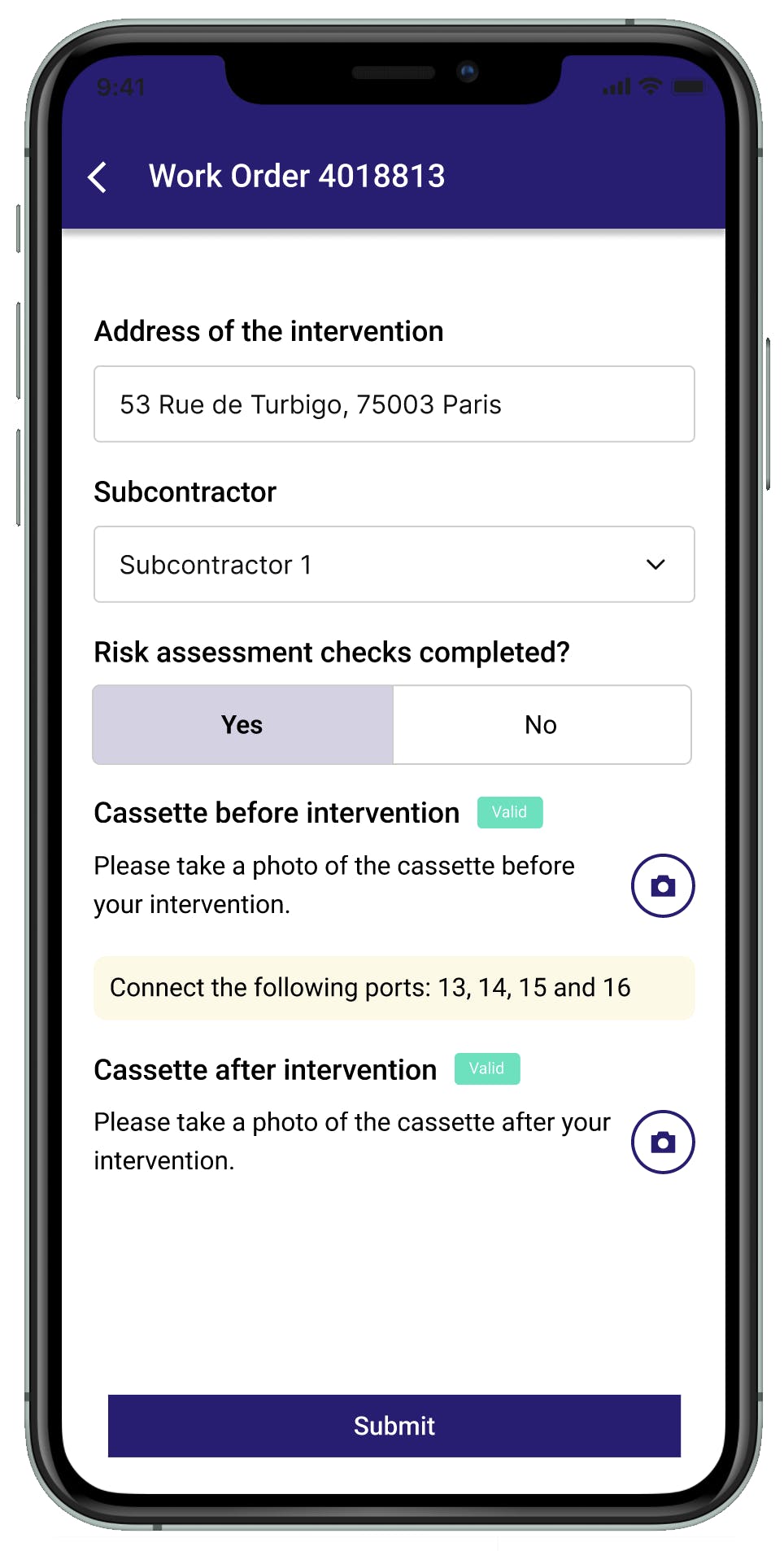
Video of the field experience created thanks to Camera Connector
Reporting experience true to field reality
Technicians may work on multiple assets within the same operation. Each of these is sometimes required to provide various types of data: address or geo-location, equipment identifier, materials used, PDF documents, photos before and after work, etc. By deploying Deepomatic's computer vision solution via Camera Connector, companies create a journey where the technician navigates seamlessly between their field application and Deepomatic's to provide the necessary data to document the operation. The reporting experience becomes more comprehensive and representative of field reality.
Concretely, for each step of their field operation, the technician fills out forms or data reports in their field application and switches with a click to Deepomatic's interface to start the real-time photo-taking and quality control process described earlier. The results of Deepomatic's analysis are directly transcribed in the field application through the appearance of "Valid" or "Invalid" messages next to each step of the operation.
Camera Connector allows field service companies to enhance operation reporting without adding friction to the technicians' experience. This new connector also enables them to create a user experience that contributes to accelerating the value generation they derive from our computer vision platform.