Quality Control Automation
Revolutionize field inspection with real-time quality control automation. Make sure you have a clear and accurate record of what happens in the field.
Modern field tools assist in planning, but they fall short in ensuring tasks are executed correctly the first time. Deepomatic’s Visual AI gives you the means to streamline field inspections using real-time quality control automation.
- Verify work instantly and eliminate anomalies that previously led to costly revisits.
- Ensure accurate documentation with automated reporting that reflects the true work done in the field.
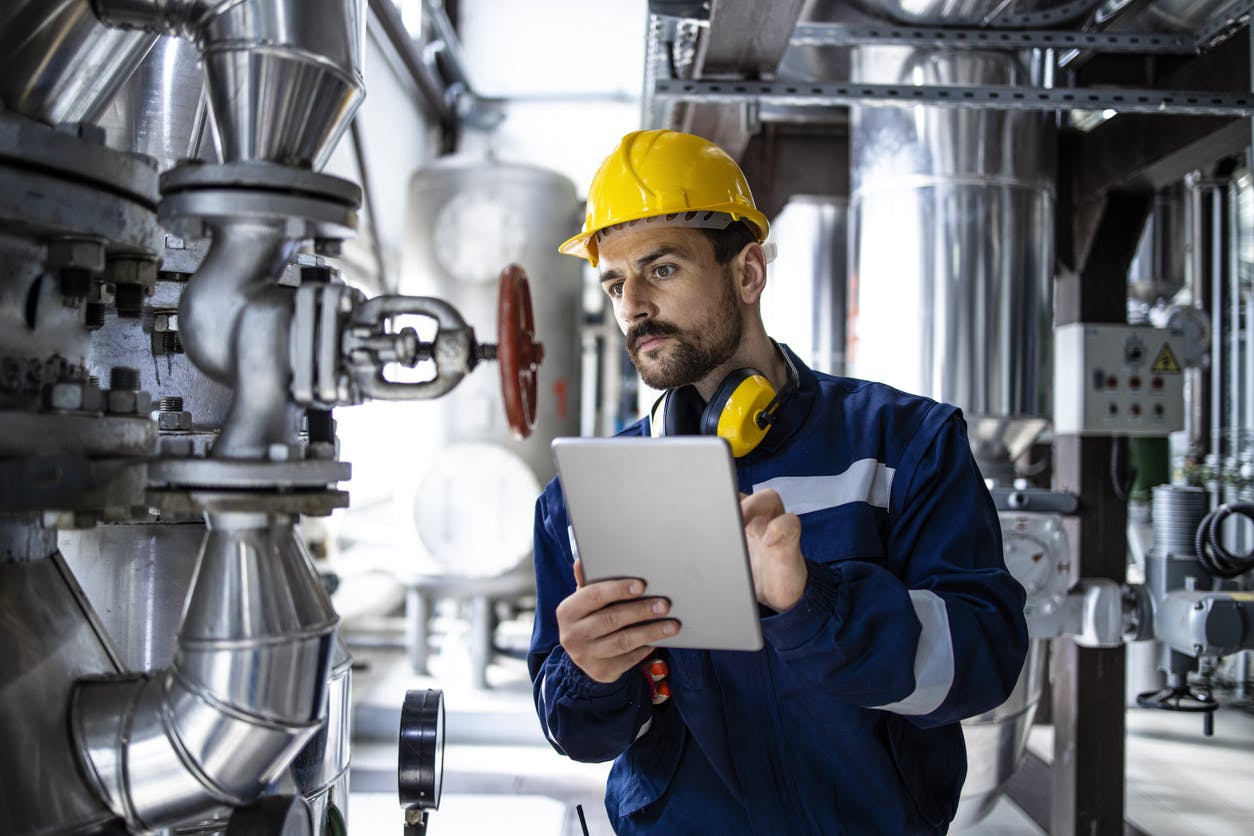
Scale Your Field Inspection Process with Quality Control Automation
With Deepomatic, enter a new dimension where 100% of field operations are instantly verified. Our AI-powered solution analyzes photos taken by field workers, ensuring they align with documentation and workmanship standards. If discrepancies arise, workers receive immediate feedback, allowing them to correct issues on-site, reducing errors and improving efficiency.
Accelerated time-to-revenue
- Faster infrastructure deployment and service activation for operators.
- Improved order-to-cash processes for contractors.
Lower costs
- Fewer re-interventions
- Lower quality control and back office costs
- Reduced costs linked to equipment damage
- Reduced penalties
Enhanced customer satisfaction
- Operators provide a higher-quality service, boosting end-customer satisfaction.
- Contractors maintain strong relationships with operators by delivering consistently high-quality results.
Reliable documentation
- Instant validation of as-built photo reports for faster build acceptance.
- Comprehensive and trustworthy closeout packages.
Offer your Field Workers a Seamless Automated Quality Control Experience
Field workers capture before-and-after photos of their tasks, and Deepomatic’s Visual AI instantly verifies their accuracy. In seconds, they receive clear feedback, ensuring compliance with quality standards.
- Workers leave the site confident their job is done right.
- They become integral contributors to the development of reliable and sustainable infrastructures.
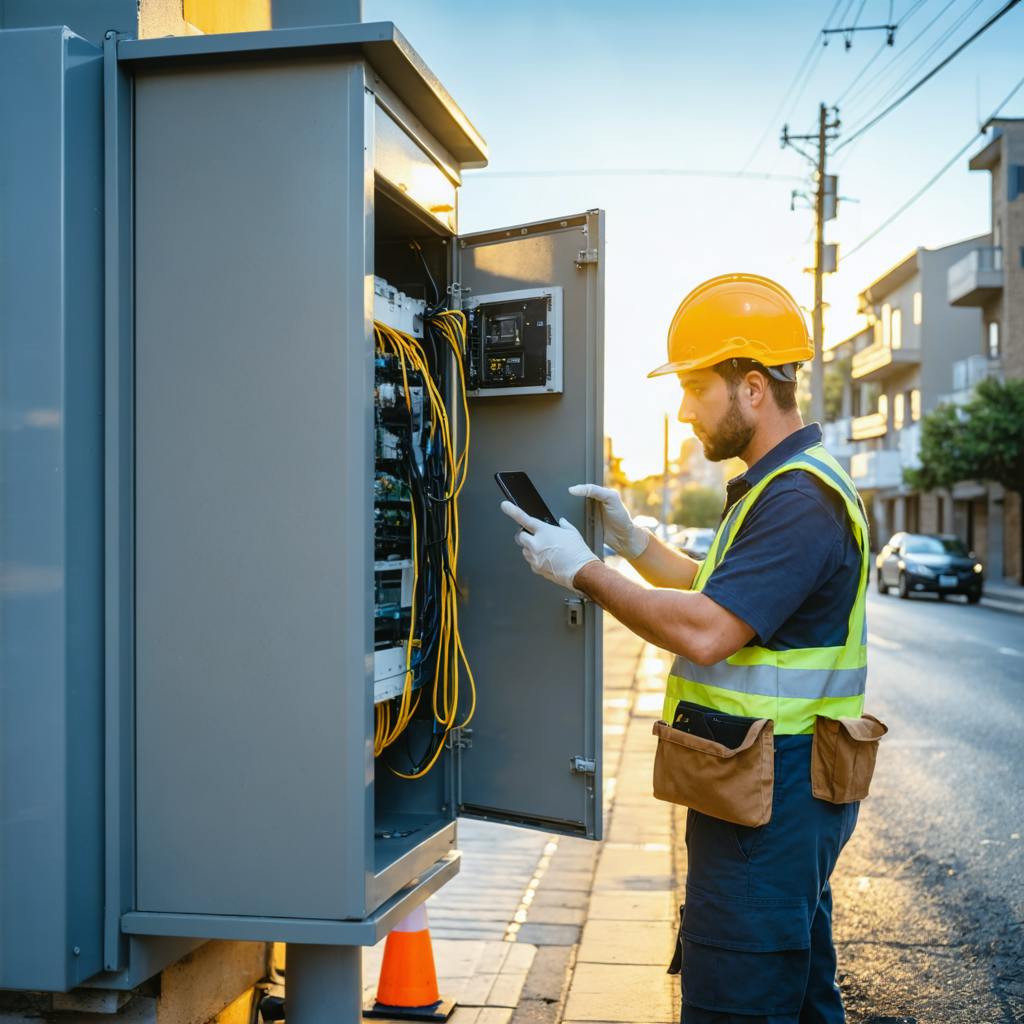
Quality Control Automation Deployed in a Mobile Experience
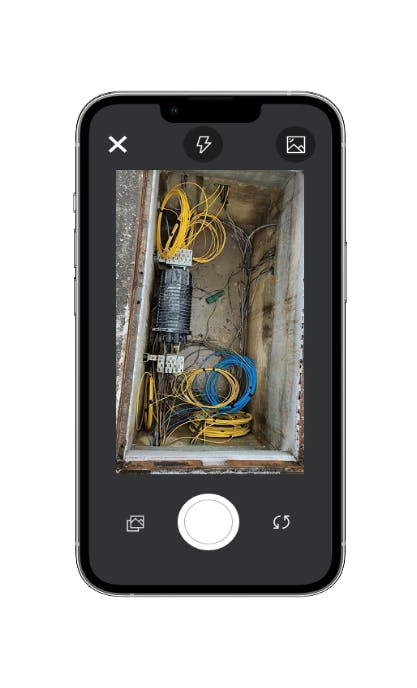
Photo capture
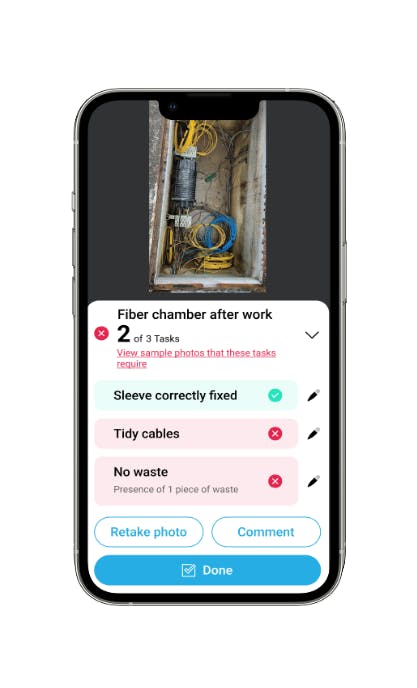
Job errors detected
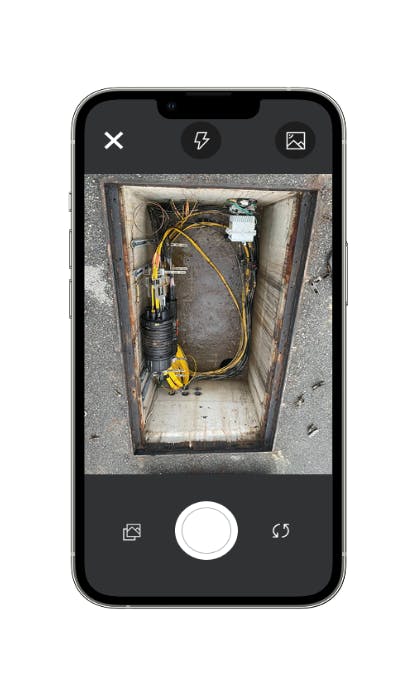
New photo capture
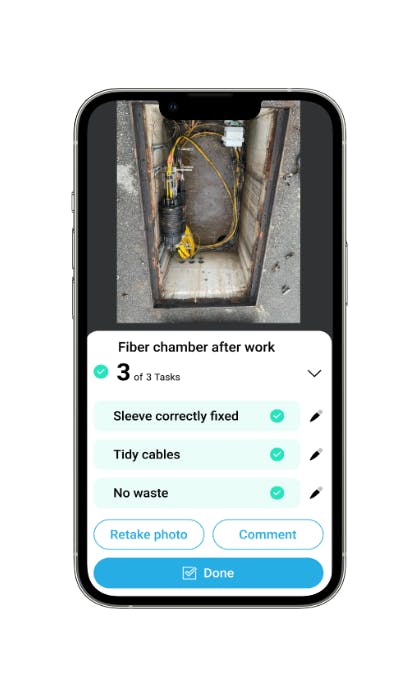
Job tasks validated
The need for Quality Control Automation
What is Quality Control Automation in Field Inspection?
Quality Control Automation in field inspection refers to the use of AI-driven tools, like Deepomatic’s Visual AI, to instantly verify the accuracy of fieldwork. By analyzing real-time images, the system ensures that every task meets documentation and workmanship standards—without manual oversight or delay. Thanks to this automated process, companies no longer have to send auditors on site to check samples of operations. The verification is handled by AI and done while the worker is still on-site.
Is Quality Control Automation Suitable for All Types of Field Operations?
Whether it's telecom infrastructure, utility installations, or other field-based services, Quality Control Automation can be adapted to various inspection needs. It ensures consistent quality, accurate documentation, and a seamless experience for field teams across industries.
How Can Companies Implement Quality Control Automation?
There is a series of steps to follow to implement an AI-powered system for quality control automation in field operations. Deepomatic created a guide to help you see clear in this process.
Implementing Deepomatic’s quality control automation is a streamlined process designed to minimize disruption to your existing operations. Following our methodology built on 10 years of experience, companies can transition smoothly to a robust quality control automation system.
Deepomatic recommends a structured integration journey that includes data collection, AI training, solution integration, and change management. By following this approach, companies can have the Deepomatic platform live and operational within three months. This systematic implementation ensures that all quality management requirements are met and that the system supports the organization's business objectives.